Application of 3D scanning spray
by M. Montalti, Sales Development Engineer Reflecon, MR Chemie
The ideal application is a homogeneous matting layer and a compromise between various requirements:Necessary layer thickness: An reflective or shining surface requires a thicker layer than a black surface.
Necessary sublimation time: A thinner layer sublimates faster than a thicker one.
Measurement uncertainty of the scanner: It is easy to understand that a layer thickness of a few micrometers hardly influences the measurement result if the scanner used has a greater measurement uncertainty.
Software: Depending on the mode and settings of the software used, which converts the generated point cloud into a 3D object, outliers can be smoothed out, but the measurement result can also be falsified.
How do we determine the layer thickness of the REFLECON 3D scanning spray?
In order to evaluate the layer thickness and the homogeneity of the application of our 3D scanning spray, we carried out a series of tests with a 4K digital microscope from Keyence from the VHX series. The microscope is capable of detecting height differences in the measuring range under consideration. To do this, we sprayed glass plates once “very thin” and once “very thick”, which were then measured. This process was repeated with all scanning sprays and an attempt was made to keep the respective “very thin” and “very thick” application at the same level as far as possible in order to achieve comparable results. As the application from a hand-held aerosol can is not reproducible, the results only provide a guide.
Below you can see how we define a “very thin” and a “very thick” application in the test. We worked with REFLECON Tarnish 11 from the aerosol can. A similar series of tests with our container products and a spray gun will follow at a later date.
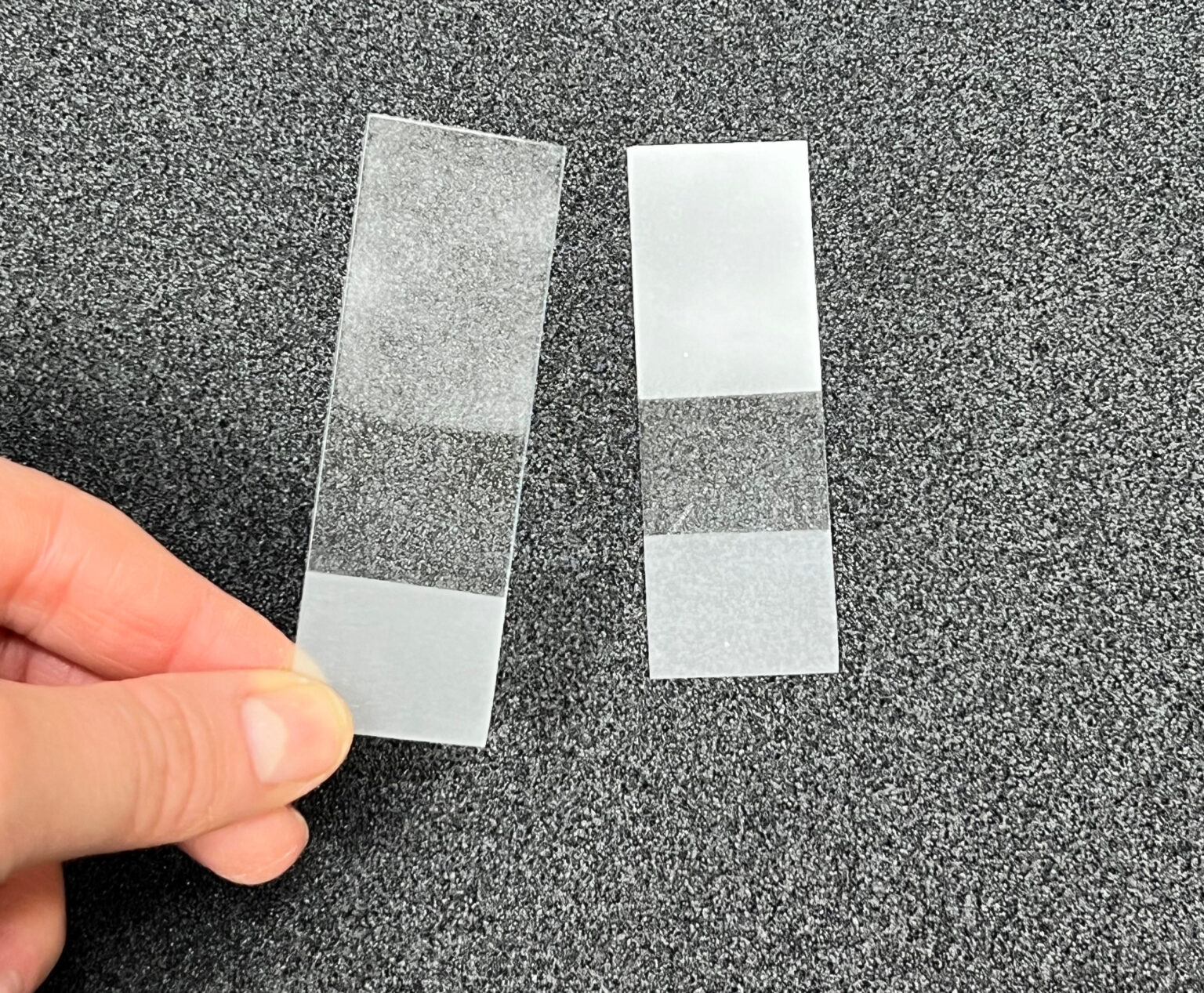
What layer thickness of the REFLECON 3D scanning spray did we determine?
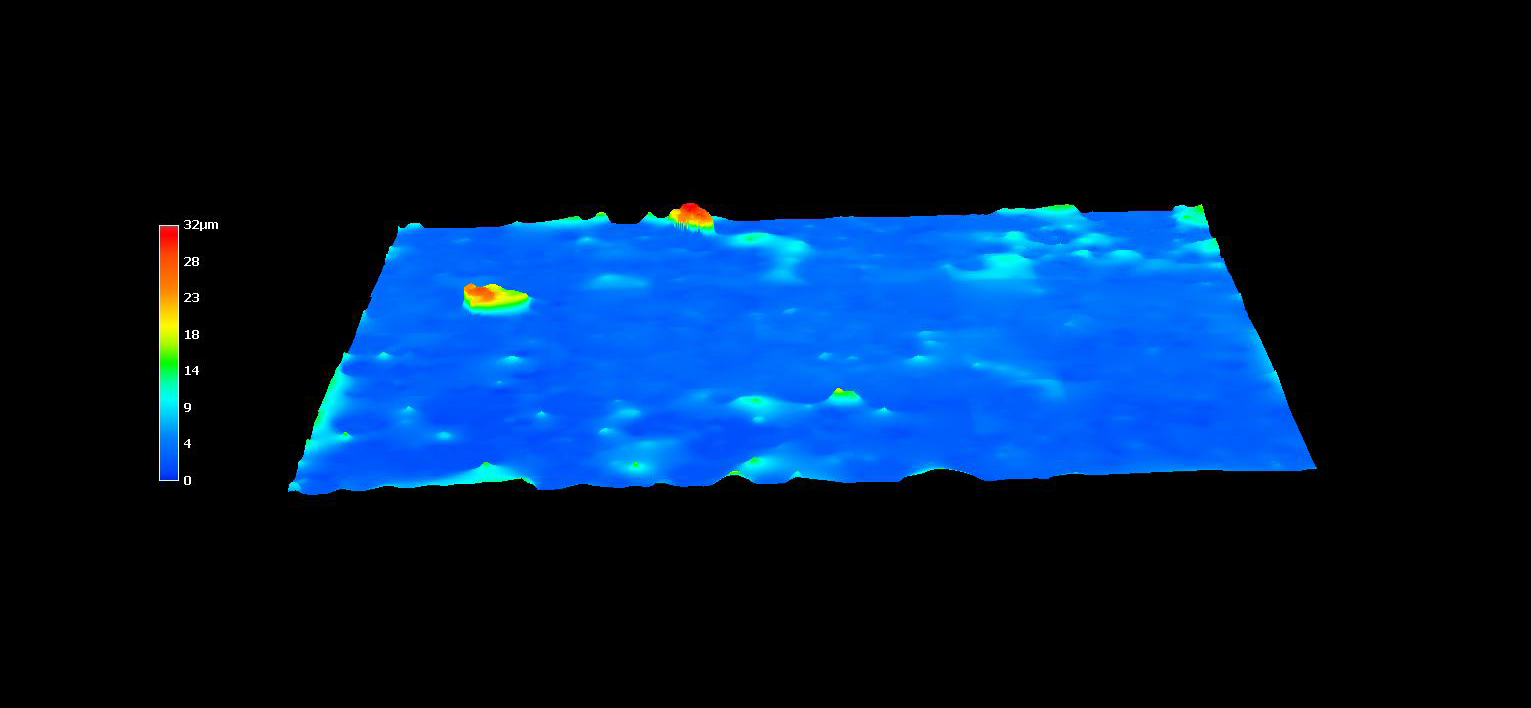
The microscope creates a color map showing the different heights of the applied layer. The scale on the left shows that dark blue stands for a layer thickness < 4 μm. Light blue, green and yellow are followed by the red range up to 32 μm. In our measuring range, we can see a few yellow and red dots in the range of 18-32 μm, some in the light blue to green range of 14-18 μm and predominantly a dark blue colored area with < 4 μm. We recognize a very homogeneous layer with few outliers.
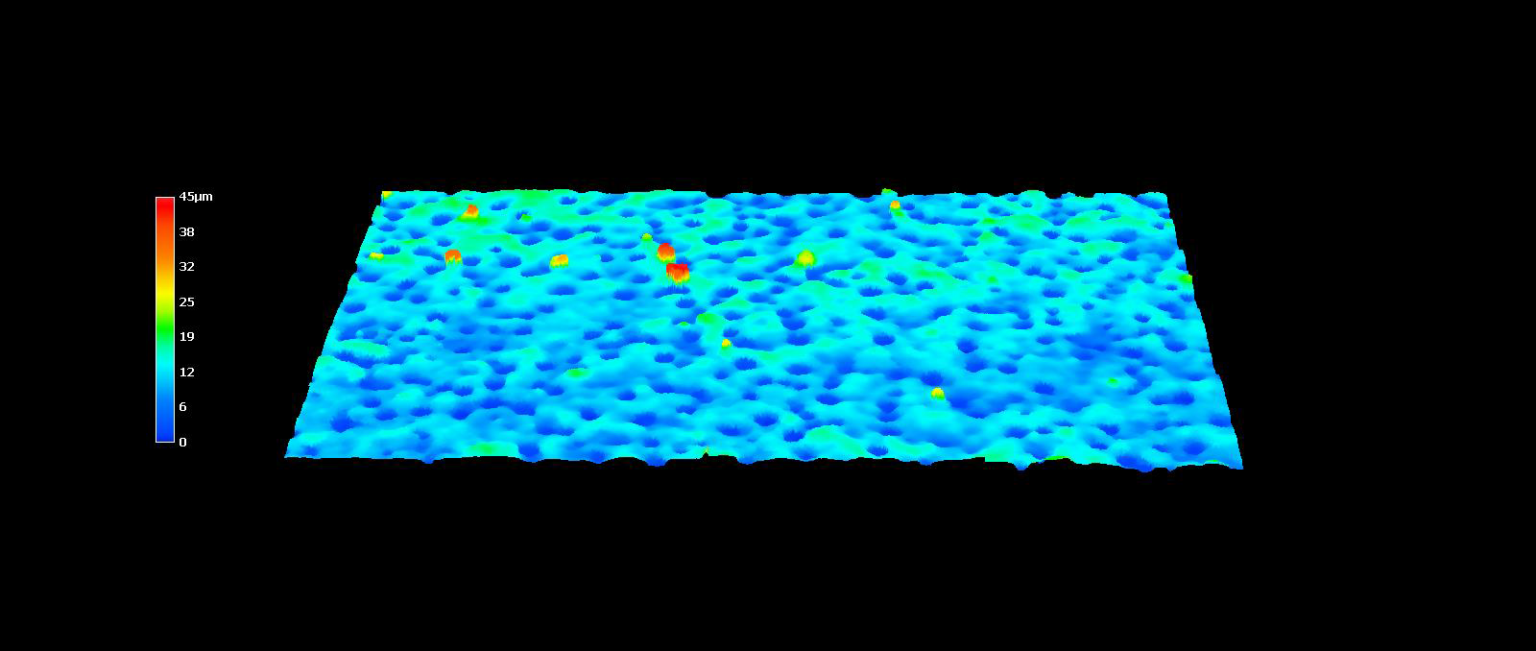
The measurement results of our other scanning sprays can be found in the respective product information.
Master the application of the 3D scanning spray
You are currently viewing a placeholder content from YouTube. To access the actual content, click the button below. Please note that doing so will share data with third-party providers.
More InformationYour contact
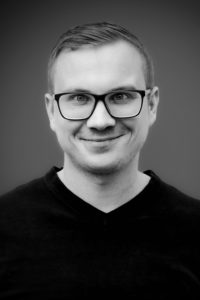
Mario Montalti
Sales Development Engineer Reflecon
0160 94750556
m.montalti@mr-chemie.de