Sticking and removing reference points - an enormous time waster
by M. Montalti, Sales Development Engineer Reflecon, MR Chemie
For sure you will know enough applications in which reference points need to be sticked on in order to digitise an object, even if you are not working with a laser scanner. Depending on the geometry or texture of the object, a 3D scanner may have problems to orientate itself during the scanning process and lose tracking. In the best case scenario, tracking losses mean that the object cannot be digitised at all. In the worst case, you as the user will not realise that the scanner is not capturing the object correctly due to tracking problems and the associated software transfers the potential error through triangulation to the CAD model. As a result, the scan of a car's rear spoiler, for example, can deviate by several centimetres.
Tracking - Don't lose your orientation
You can imagine the following for a better understanding: A rear spoiler of a car looks the same on the left side, in the centre and on the right side. A 3D scanner takes photos of the component and has the task of placing them exactly next to each other in order to obtain the correct length of the spoiler. If it loses tracking in the process, it can happen that the different images overlap. As a result, the scanned spoiler would be shorter than it actually is.
The photos below show an object that looks the same everywhere, similar to a rear spoiler, without changing geometries or textures. The scanner, in this case an Artec EVA, has lost tracking and incorrectly lined up the different images so that the actually straight sections in the scan are superimposed and shifted.
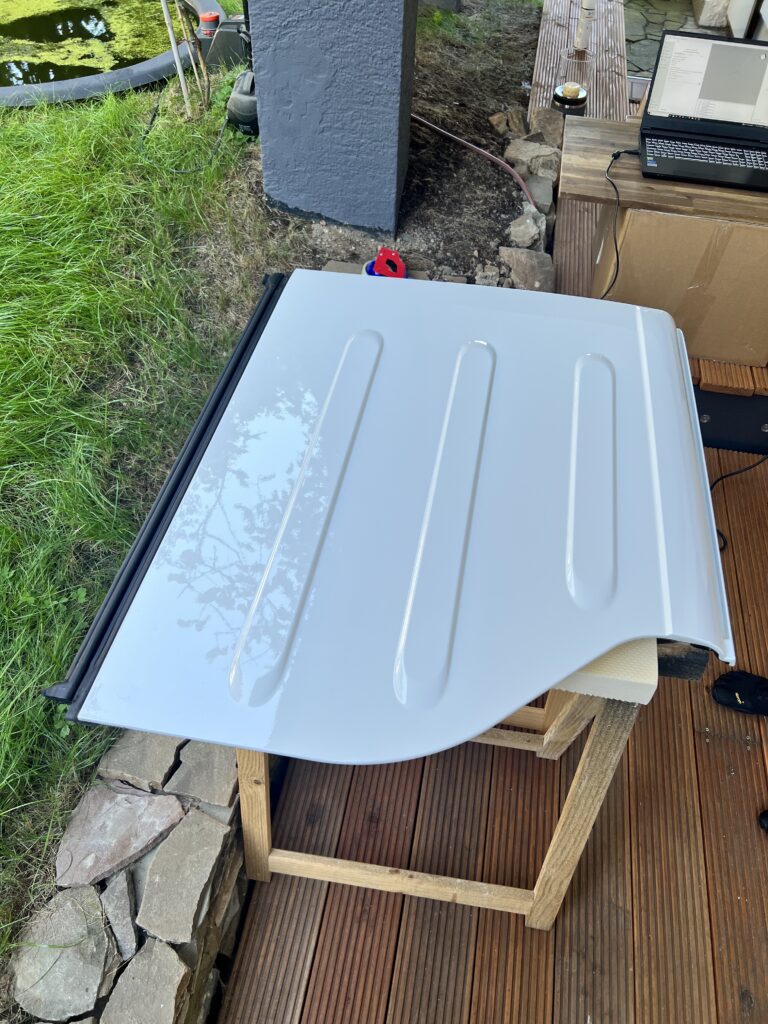
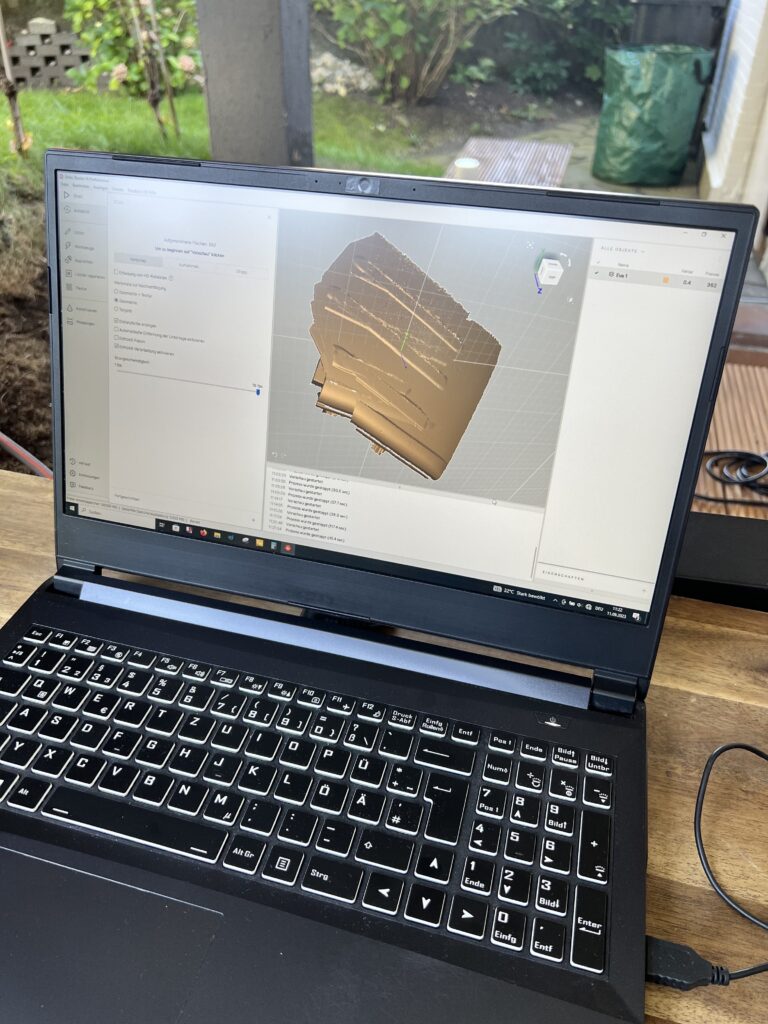
To prevent this, reference points are used to support the scanner. You will agree that sticking on and removing the reference points are the biggest time wasters in the entire scanning process. Nothing takes longer than the preparation and rework.
Solution - Reflecon TopoTrack: Quick and easy
The Reflecon TopoTrack 2in1 Scanning Spray was developed to significantly minimise the process time of a 3D scan. The process time is not only reduced by eliminating the need to stick on and remove reference points, but also because you can guide your scanner over the object much faster. In addition to classic matting, which is particularly necessary for transparent, shiny and highly reflective objects, it also offers tracking support thanks to its special structure, meaning that reference points or other aids are no longer required! The spray sublimates and has a very long service life of 12-24 hours, making it ideal for large objects. Subsequent cleaning of the objects is not necessary.
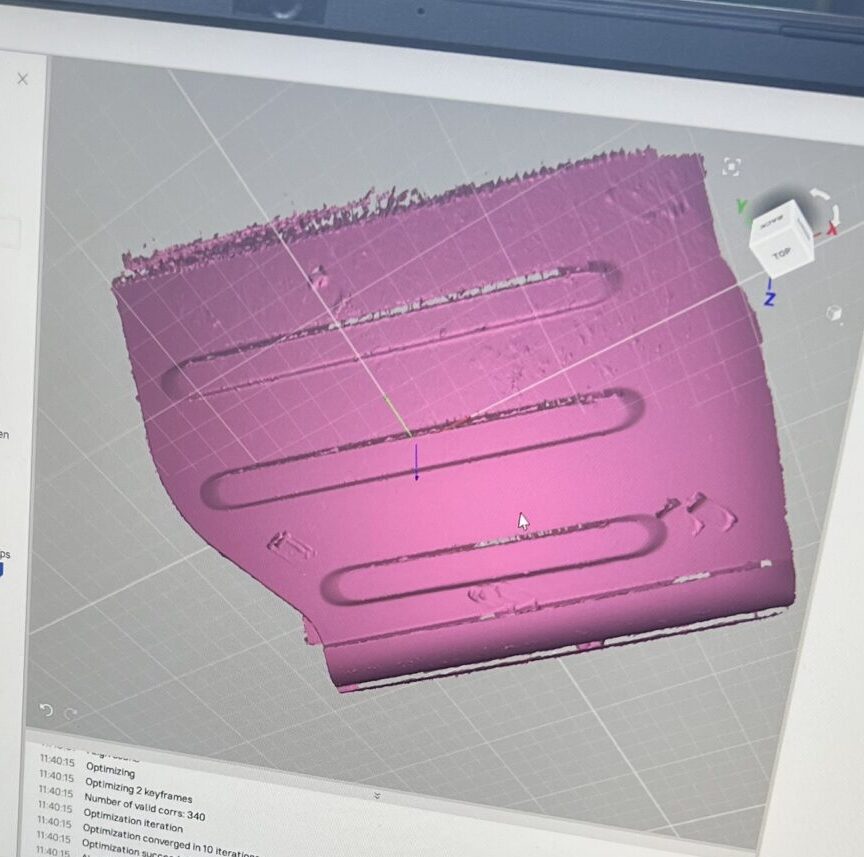
But how does it all work? The name TopoTrack is made up of two words: “topography” and “tracking”. The spray forms a topographical layer that resembles the structure of woodchip wallpaper when viewed under a microscope. Based on this randomly changing structure, a high-resolution scanner is able to orientate itself.
The layer thickness of the spray is a maximum of 35μm for a single application, making it suitable for most applications, especially for large objects. The graphic below shows how the spray forms a homogeneous structure of “mountains and valleys” over the entire surface.
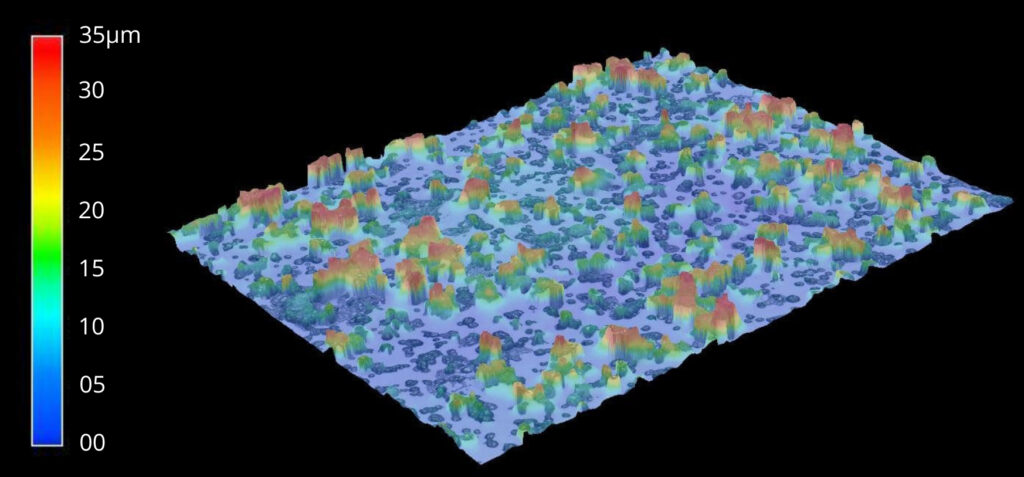
Application - Which scanners is the TopoTrack suitable for?
In order to be able to recognise the 0-35μm structure, we recommend using a high-resolution scanner with slight overexposure. Texture support should be activated.
TopoTrack also allows you to perform measurement tasks with low-cost scanners for which you would normally need a higher-quality scanner.
The following scanners in particular receive a noticeable update in combination with TopoTrack:
- Artec EVA
- Artec Spider
- Shining Einstar
- Shining EinScan H und H2
- Shining Combo im IR Modus
LED, White light and infrared light scanners with a small field of view benefit the most, as they have less chance of detecting geometries or textures of the object in their measuring field. Laser scanners, on the other hand, require reference points for systemic reasons.
Practical examples
The following videos show and describe the use of TopoTrack very well:
Your contact
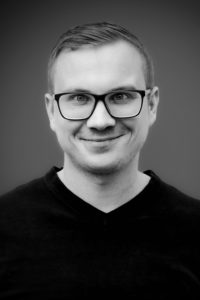
Mario Montalti
Sales Development Engineer Reflecon
0160 94750556
m.montalti@mr-chemie.de