Instructions for optimizing the 3D scan results
by M. Montalti, Sales Development Engineer Reflecon, MR Chemie
3D scanning has established itself as an indispensable technology in many industries, from the automotive and aerospace industries to medical technology. MR Chemie GmbH's Reflecon 3D scanning sprays are key tools for achieving precise and detailed scanning results at high speed.
In this article, we offer a comprehensive guide to optimising 3D scanning results with the various Reflecon 3D Scanning Sprays and talk about preparation, application, common challenges and their solutions, as well as technical insights.
Preparation and application tips
1. Surface preparation
Make sure the surface is clean and free of dust, oil and other contaminants. Thorough cleaning of the surface with suitable cleaning agents ensures an even and stable coating of the scanning spray to maintain the correct surface tension. Coarse dust can distort your measurement results, greases and oils can influence the sublimation time or even prevent sublimation as they could close around the matting agent.
2. Application of the scanning spray
Firstly: The cans of sublimating sprays do not contain mixing balls, so they do not need to be shaken. You can start spraying immediately.
The correct application of the scanning spray is crucial for an even coating and therefore for precise scanning results. Hold the spray can at a distance of about 20-25 cm from the surface and move the can evenly to create a homogeneous layer. Do not “paint” your components but carry out short sprays loosely from the wrist. Always spray in an even movement and avoid lingering too long in one place. This prevents the formation of drops and ensures an even layer.
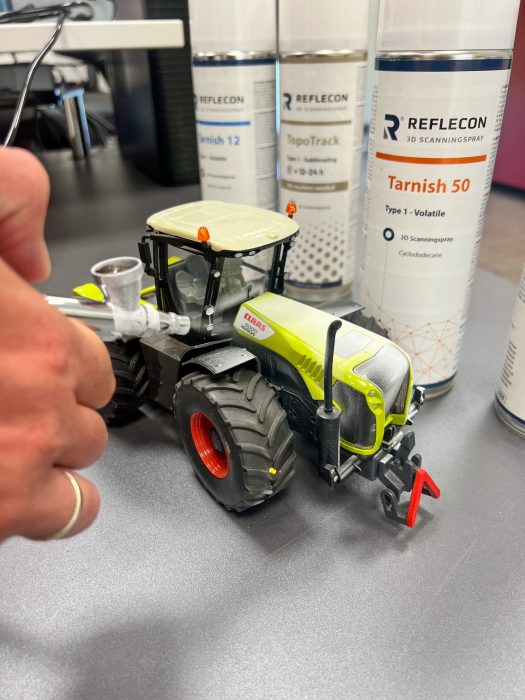
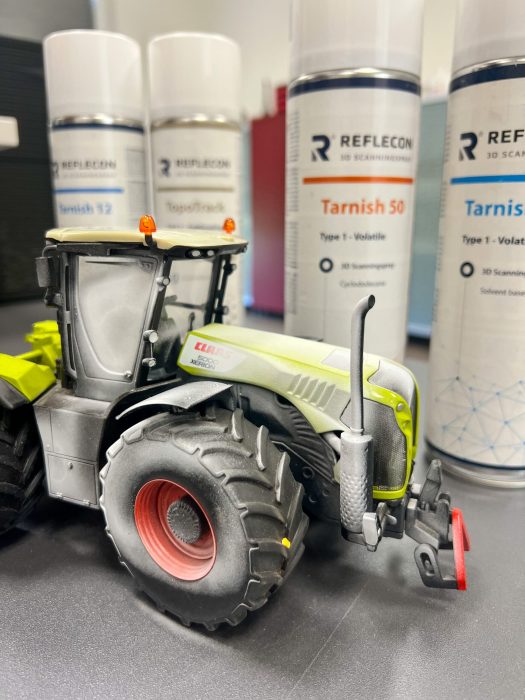
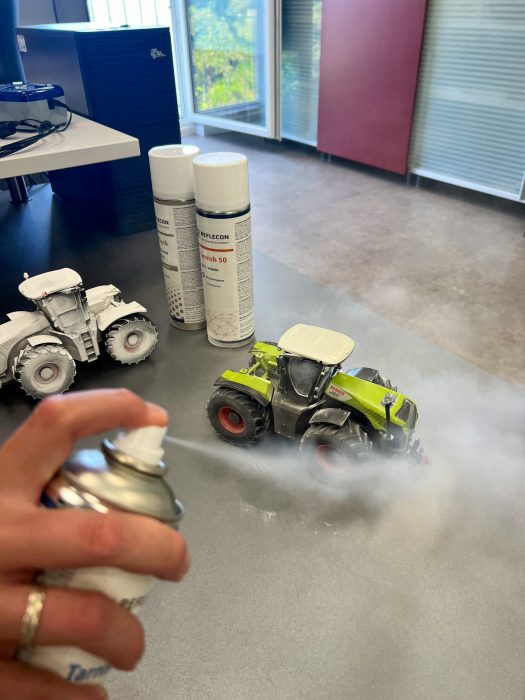
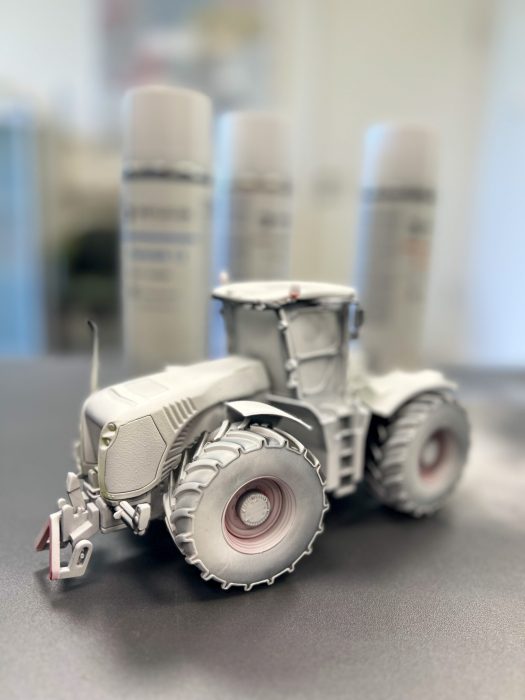
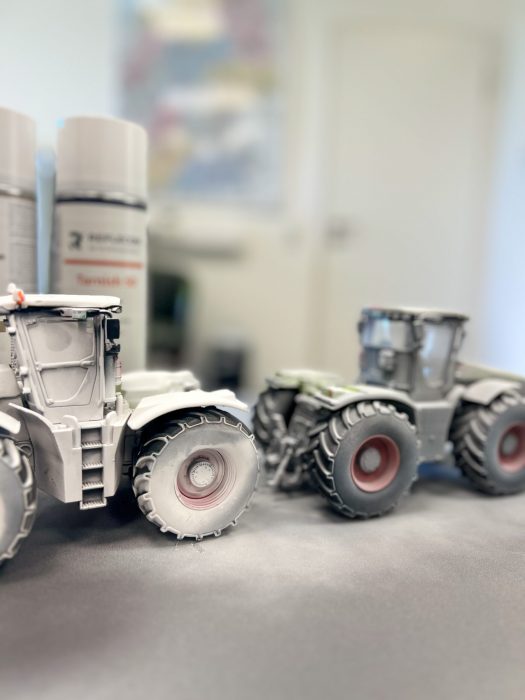
3. Layer thicknesses
Depending on how the scanning spray is applied, layer thicknesses of just a few μm can be achieved, which have hardly any influence on the dimensional accuracy of the scanning result. Further details on this topic can be found in the separate article: Application and layer thicknesses of REFLECON 3D scanning spray – MR Chemie (mr-chemie.de)
4. Drying time and scanning
Wait until the coating is completely dry before you start scanning. The drying time may vary depending on the ambient temperature and the thickness of the coating applied. A completely dry coating ensures optimum matting and therefore accurate scanning results.
5. Avoid overspray
To avoid overspray that could wet neighbouring areas, use masking materials such as foil or paper towels to cover adjacent surfaces. This helps to limit the spray layer to the desired surface only.
Common challenges and solutions
1. Uneven coating
An uneven coating can have a negative impact on the scan results. This can be caused by improper application, inadequate surface preparation or incorrect spacing when applying the spray. To avoid this, clean the surface thoroughly and maintain the recommended distance. Move the spray can evenly with short sprays to create a thin homogeneous layer.
2. Compatibility with different materials
Our Reflecon 3D scanning sprays are suitable for a wide range of materials, including metals, plastics, glass and ceramics. Before use, study our material compatibility chart (t_comparison_table_material_compatibility_EN.indd (mr-chemie.de)) to find out which spray and material combination is or is not compatible. If you are unsure, test the spray on a small area first to make sure it will not have a negative effect on the material. Some materials, especially plastics or painted components, can react sensitively to the solvents contained in the spray. It is therefore advisable to carry out a test beforehand. To do this, spray an area, wait two minutes and then wipe off the matting agent with a dry cloth. If there is a chemical reaction, it will occur immediately. If you do not notice any surface damage, no reaction is to be expected even if the agent is left on for a longer period of time.
This advice is generally valid, as scanning spray cans always contain solvents, regardless of the manufacturer.
3. Residues of the scanning spray
Our scanning sprays sublimate completely and leave no residue, provided that the material compatibility and surface cleanliness are given. They have therefore been approved by a lot of companies in the automotive and aerospace sectors following internal tests by the respective customers. After sublimation, the components can be further processed, welded or painted without any problems.
Technical insights
Factors influencing the sublimation time
- Temperature: Higher temperatures shorten the sublimation time of the spray, while lower temperatures lengthen it. It is important to consider the ambient temperature and make adjustments if necessary. An insider tip is to cool cans, e.g. in a refrigerator, to give the medium a longer sublimation time.
- Surface texture: Rougher surfaces increase the sublimation time, while smoother surfaces shorten it. This is because the solvents can linger longer in the recesses of rough surfaces
- Air circulation: Circulating air or wind accelerate sublimation considerably. However, this effect can also be used, for example, to reduce the sublimation time in exceptional cases with the aid of a hairdryer.
- Storage: Store the scanning sprays at temperatures between 5°C and 45°C. Ensure that the cans are protected from direct sunlight and extreme temperatures. The minimum shelf life is three years.
Your contact
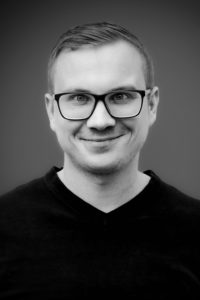
Mario Montalti
Sales Development Engineer Reflecon
0160 94750556
m.montalti@mr-chemie.de