Modern UV LED technology facilitates fluorescent penetrant testing in NDT
Importance of non-destructive testing for the industry
Non-destructive testing (NDT) plays an essential role in safety-critical industries such as aviation, automotive engineering, power generation, mechanical engineering and medical technology. It makes it possible to detect material and manufacturing defects without damaging components. A particularly well-established method is fluorescent penetrant testing, which makes the finest surface defects visible. The quality and effectiveness of this process depends heavily on the UV light source used, among other factors.
In the past, mercury vapor lamps were mainly used. However, these have serious disadvantages, including long warm-up times, high temperatures and low energy efficiency. Modern UV LED technology offers a significant improvement here. One of the most innovative developments in this area is the use of UV LEDs, which were developed specifically for industrial testing applications.
Challenges for UV light during fluorescent crack detection
Fluorescent penetrant testing is a highly sensitive process that depends on several factors:
- Sufficient UV intensity: The fluorescence of the penetrant must be optimally stimulated.
- Uniform light distribution: Homogeneous irradiation prevents false negative results.
- Low proportion of white light: Too much visible light can reduce the contrast of the fluorescent displays.
Outdated light sources or inferior UV LEDs can lead to even critical defects not being detected. Standards such as ASTM E3022, the Rolls-Royce specification RRES 90061 and DIN EN ISO 3059 therefore place strict requirements on UV lights in testing technology.
Important basics of UV light application
Fluorescent penetrant testing uses the principle of fluorescence:
- A fluorescent penetrant penetrates into fine cracks or pores.
- Excess agent is removed.
- Under UV light (approx. 365 nm), the agent remaining in the defects begins to glow.
The quality of the test is influenced by the following physical factors:
- Wavelength: Optimal fluorescence excitation occurs at 365 nm.
- Irradiance: Values between 1,000 and 4,500 µW/cm² are specified in the ASTM E3022 standard. DIN EN ISO specifies at least 10Watt/m² (=1000µW/cm²) and less than 50W/m² (=5000µW/cm²) is recommended for the penetration test.
- Surface finish: Shiny surfaces can cause reflections that impair the visibility of the displays.
Modern UV LED technology vs. conventional light sources
UV LED lights use state-of-the-art LED technology to overcome the challenges of conventional UV light sources. The advantages of modern UV LED lights compared to traditional mercury vapor lamps are enormous:
Property | Mercury vapor lamps | UV LED lights (e.g. MR® 975) |
Warm-up time | Up to 10 minutes | Immediately ready for use |
Service life | 1,000-2,000 hours | 10,000+ hours |
Energy consumption | High | Low |
Heat generation | Very high | Low |
Environmental compatibility | Contains toxic mercury | No environmentally harmful substances |
These technical improvements enable companies to reduce their operating costs and increase inspection reliability at the same time.
Risks associated with sub-optimal UV testing methods
Incorrect or inferior UV light sources can cause serious problems:
- Undetected cracks or material defects lead to dangerous component failure.
- High rework costs due to incorrect test results.
- Safety risks in industries such as aviation or mechanical engineering.
- Unnecessary production delays due to inefficient testing processes.
A concrete example of the industrial use of UV technology in crack testing is the automotive industry: here, fluorescent magnetic particle testing is used to visualize surface cracks on safety-relevant components such as axles or crankshafts. The component is magnetized and wetted with a fluorescent testing agent. Cracks cause stray fields on which particles collect. Under UV-A light, these accumulations become visible – even the finest cracks light up clearly.
The method enables fast, reliable and highly sensitive testing on an industrial scale. Early defect detection prevents accidents, increases product quality and reduces production downtime. This non-destructive testing method is used to detect surface cracks and material defects in safety-relevant components such as axles, crankshafts or steering components.
The MR® 975 UV LED lamp from MR Chemie
The MR® 975 is a powerful UV LED lamp that has been specially developed for the high demands of fluorescent crack detection. Their most important features:
- Wavelength of 365 nm for optimum fluorescence excitation.
- Irradiance of up to 4,500 µW/cm², adjustable as required.
- Low white light component below 5 lux to display contrasts optimally.
- Robust aluminum housing and rubber protection ring, ideal for harsh industrial environments.
- Switch between UV and white light at the touch of a button for flexible inspections.
- Compliance with the ASTM E3022 and Rolls-Royce RRES 90061 standards as well as DIN EN ISO 3059 for the highest quality standards.
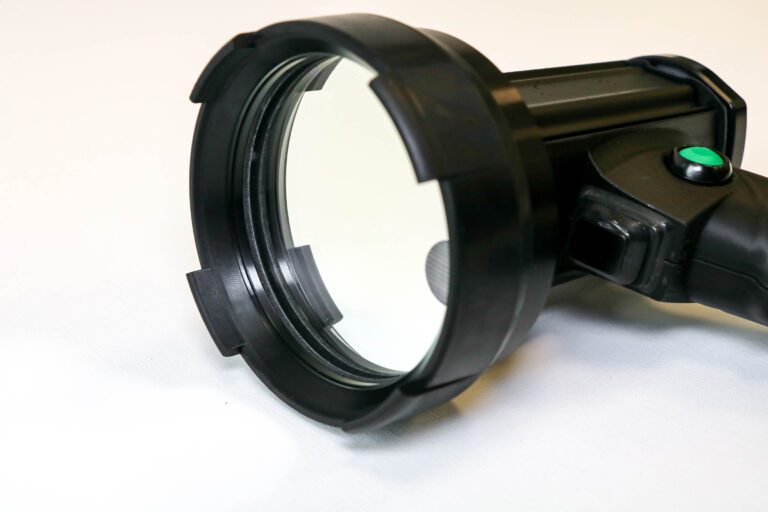
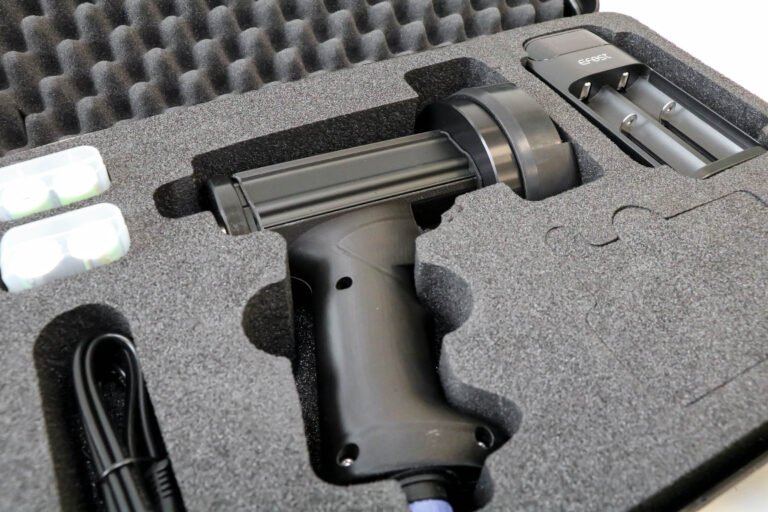
Conclusion: The future of UV testing with the MR® 975
UV LED technology has revolutionized non-destructive testing. Companies that rely on modern UV LED lights such as the MR® 975 benefit from greater inspection reliability, more efficient processes and lower operating costs.
The future of NDT lies in innovative technologies that combine accuracy, energy efficiency and environmental compatibility. The MR® 975 from MR Chemie is the perfect solution for companies that want to meet the highest quality standards and optimize their testing processes.